Carbon (CFK): Den Superwerkstoff erklärt
Carbon, das schwarze Gold
Geringeres Gewicht bedeutet weniger Verbrauch und höhere Performance. Deshalb hält der Superwerkstoff Carbon (oder CFK) mehr und mehr Einzug im normalen Automobilbau.
Was im Rennsport seit Jahrzehnten gang und gäbe ist, findet nun in verstärktem Maße auch in der Serienfertigung von Autos Verwendung: kohlefaserverstärkter Kunststoff, kurz CFK oder Carbon. Hohe Festigkeit und Steifigkeit bei geringem Gewicht empfehlen die Wunderfaser für mechanisch stark belastete Bauteile wie Karosserien, Räder und selbst Fahrgastzellen. Auch interessant: Unsere Produkttipps bei Amazon
Leslie & Cars fährt die Porsche GTS-Modelle (2022) im Video:
Diese Vorteile hat Carbon
CFK-Teile sind im Vergleich zu denen aus Stahl um 50 und zu denen aus Aluminium um 30 Prozent leichter. Im Gegensatz zu den beiden Metallen, deren Werkstoffeigenschaften in nahezu jeder Belastungsrichtung gleich sind, ist bei CFK die Faserausrichtung für die Bauteileigenschaften maßgebend. Der Grund: Das Gewebe weist zwar hohe Zugfestigkeitswerte, jedoch nur eine geringe Belastbarkeit in Druckrichtung auf. Zu beachten sind beim Carbon daher vor allem die Formgebung der Bauteile sowie die Materialbelegung, sprich die Anordnung der Gewebelagen. Richtig eingesetzt, kann es beim Auto jedoch entscheidende Vorteile im Gewicht bringen – vom im Tuning beliebten Carbon-Look ganz zu schweigen.
Auch interessant:
Bearbeiten von Carbon
Lange war Kohlefaser nur mit sehr hohem Aufwand zu bearbeiten, was den Einsatz von Carbon beim Auto zumeist auf teure Kleinstserien im Rennsport beschränkte. Bei der Herstellung eines Monocoques für einen Formel 1- oder Langstrecken-Rennwagen aus Carbon sind beispielsweise zunächst ein Modell und danach eine oder mehrere mehrteilige Formen zu bauen. Das bereits mit Harz getränkte Kohlefasergewebe (sogenanntes Prepreg) wird im ersten Fertigungsschritt in die Form gelegt. Diese kommt danach in einen luftdichten Sack, in dem über eine Vakuumpumpe ein Unterdruck erzeugt wird, damit keine Lufteinschlüsse im Kohlefaser-Laminat entstehen. Im nächsten Schritt wird das Teil unter einem Druck von bis zu zehn bar und bei Temperaturen um 120 °C gebacken. Dieser aufwendige Prozess eignet sich freilich in keiner Weise für größere Stückzahlen, wie sie bei einer Serienfertigung von Autos anstehen.
Aus diesem Grund wurde das RTM-Verfahren (Resin Transfer Moulding) entwickelt. Hierbei werden Lagen des Kohlefaser-Gewebes, die im Gegensatz zum Prepreg-Verfahren noch nicht mit Harz getränkt sind, mit einem Presswerkzeug vorgeformt. Die Vorformlinge werden anschließend mittels einer Injektionsanlage mit Harz getränkt und unter Druck und Temperaturen um 100 °C ausgehärtet.
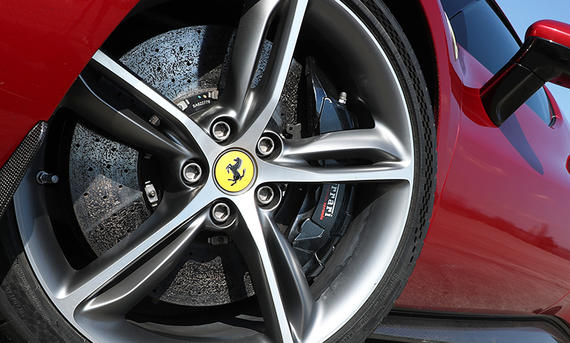
Ungefederte Massen verringern
Neben großen Werkstücken wie Carbon-Karosserien bietet auch die Herstellung von Rädern und Bremsscheiben aus leichtem CFK Vorteile – insbesondere durch die geringeren ungefederten Massen, die eine sensiblere Abstimmung der Federelemente erlauben. Außerdem verringern sie das Trägheitsmoment, was sich in einem optimierten Handling und einer verbesserten Beschleunigung bemerkbar macht. Während in der Anfangsphase der Carbon-Bremsen für Autos in den 80er-Jahren noch ein beträchtlicher Reibwert-Unterschied zwischen kalten und heißen Bremsscheiben bestand, schritt die Technik bis heute derart voran, dass für Luxus- und Sportwagen weiterentwickelte Carbon-Keramik-Bremsen sogar in Serie zum Einsatz kommen. Beispiele dafür sind der BMW M8, der Ferrari 296 GTB oder der Porsche 911 Turbo S. Neben einer verlängerten Lebensdauer lässt sich so auch wertvolles Gewicht am Auto sparen, allerdings ist die Betriebstemperatur mit diesem Werkstoff höher als bei herkömmlichen Bremsscheiben aus Stahl, womit die umgebenden Komponenten umgehen können müssen.
Nachteile von Carbon
Wo liegen – neben dem hohen Fertigungsaufwand – die Nachteile des teuren Super-Werkstoffs Carbon? Da lassen sich vor allem die niedrige Belastung in Druckrichtung und die aufwendige Schadenserkennung sowie -reparatur nennen. Konstruktiv stellen sich zudem die erhöhte Schall- und Vibrationsübertragung als besondere Aufgabenfelder. Außerdem ist Carbon kaum zu recyceln und hat eine schlechte Ökobilanz.
Geringes Gewicht, hohe Zugfestigkeit, lange Lebensdauer – Carbon (CFK) hat einige Vorteile. Der größte Nachteil ist und bleibt jedoch die teure weil aufwendige Fertigung, weshalb der Edelwerkstoff vermutlich auch in Zukunft eher exklusiven Fahrzeugsegmenten vorbehalten bleibt.